Mango Materials, an innovative company, stands out for its ability to transform methane, a greenhouse gas, into biodegradable plastics. This advancement in biomanufacturing represents a direct response to current environmental challenges, particularly plastic pollution and greenhouse gas emissions. By converting waste into a valuable resource, Mango Materials not only creates alternatives to traditional plastics but also encourages a more sustainable circular economy. This approach contributes to reducing the carbon footprint and opens new perspectives for the materials industry.
Transforming methane into biodegradable polymers

Mango Materials, a biomanufacturing company based in California, has developed an innovative process that converts methane, a potent greenhouse gas, into a biodegradable polymer called polyhydroxyalkanoate (PHA). This process uses microorganisms that consume methane to produce PHA, which can be transformed into biodegradable polyester pellets. These pellets can then be used to manufacture durable goods, fabrics, and flexible films with the practical properties of plastics, but with a significantly reduced environmental footprint.
A reduced carbon footprint
“We are working on a negative carbon process,” said Allison Pieja, co-founder and chief technology officer of Mango. Analyses indicate that this process should be negative carbon when operating at full scale. Mango’s new PHA production facility, located at a wastewater treatment plant in Vacaville, California, captures the methane produced by microbes that clean public water and introduces it directly into bioreactors with methane-consuming bacteria.
Products already on the market
Mango is already producing enough PHA to manufacture some demonstrative products, including a soap dish available for purchase, as well as two prototype products: a pair of net-zero sneakers from the brand Allbirds and sustainable sunglasses from renowned designer Stella McCartney. The company now aims to increase the production of PHA pellets to provide a diverse range of eco-friendly products.
Optimization and commercialization
Like all biomanufacturing technologies, the transition from a laboratory concept to an efficient commercial process took time. Mango collaborated with the Advanced Biofuels and Bioproducts Process Development Unit (ABPDU) to refine its bacterial cultures and optimize growing conditions to maximize the quantity and purity of PHA. This collaboration allowed Mango to test relevant industrial-scale equipment before investing in its own pilot systems.
Purification of polyhydroxyalkanoate (PHA)
Bacteria transform methane into PHA chains to store energy, similar to how plants store energy in starches. In collaboration with Ning Sun’s team at the ABPDU, Mango tested recovery equipment to maximize yields and the purity of PHA extracted from bacterial cells.
Experts serving innovation
Through this partnership, Mango gained valuable expertise in the extraction of intracellular biopolymers, and the ABPDU was able to apply this experience to other similar projects. To date, the ABPDU has collaborated with 85 industrial partners and 20 national laboratories, research centers, and universities to assist in scaling up and launching innovative products based on biology.
Mango Materials’ work at the ABPDU has been funded by grants from the U.S. Department of Energy, aimed at enabling start-up technologies in biofuels, biomaterials, and biochemical products to move from the laboratory to commercial relevance.
Benefits and Technology
Benefits | Technology |
Reduction of greenhouse gases | Use of methane-consuming microorganisms |
Production of biodegradable plastics | Conversion of methane into PHA |
Negative carbon footprint | Specialized bioreactors |
Support for clean energy | Collaboration with ABPDU |
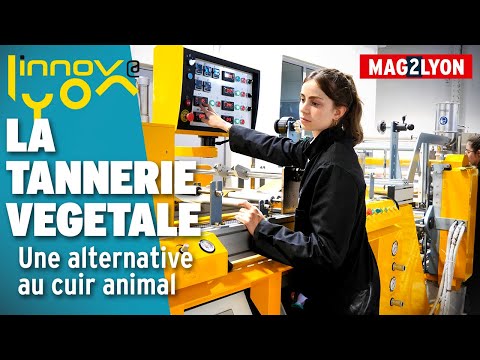
Biotechnology and biomanufacturing are key to solve some of our most pressing challenges.
— European Commission (@EU_Commission) March 20, 2024
Today, we've proposed a series of targeted actions to boost these fields.
This will contribute to create the right environment for the sector to grow and deliver global solutions.
More ↓
Articles similaires
Thank you!
We will contact you soon.